Adapting Nursery Tray Manufacturing Machine Technology for Customized Packaging Solutions
- june11433
- Apr 2
- 2 min read
The growing demand for sustainable and application-specific packaging solutions has driven innovations in molded pulp technology. A nursery tray manufacturing machine, traditionally used for producing biodegradable seedling trays, is now being adapted to create customized packaging for various industries. By modifying key aspects of its operation, manufacturers can expand its application beyond agriculture, optimizing production for food, electronics, and industrial packaging.
Precision Engineering for Custom Mold Designs
A modern nursery tray manufacturing machine employs vacuum forming and pressure molding techniques to achieve precision in shape, depth, and texture. Customization begins at the mold design stage, where advanced CNC machining allows for intricate detailing and product-specific configurations. By adjusting mold cavity dimensions and material composition, manufacturers can tailor packaging solutions to meet industry-specific requirements, ensuring both functionality and structural integrity.
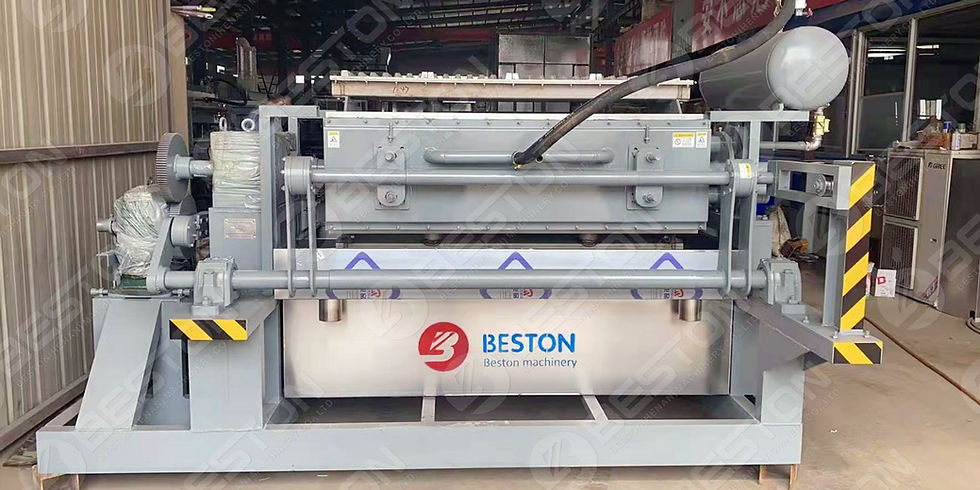
Raw Material Versatility for Sustainable Solutions
One of the key advantages of pulp molding equipment is its ability to process a diverse range of raw materials. While traditional operations rely on recycled paper pulp, innovative modifications enable the incorporation of agricultural waste fibers such as bamboo, bagasse, or wheat straw. This flexibility not only enhances the eco-friendly attributes of the final product but also provides cost-effective alternatives to industries requiring specialized packaging with sustainable sourcing.
Automation and Adaptive Production Capabilities
Customization in molded pulp packaging demands a high degree of automation to ensure efficiency without compromising quality. A fully automated nursery tray manufacturing machine integrates programmable logic controllers (PLCs) and real-time monitoring systems to adjust production parameters dynamically. Variable-speed forming, precision trimming, and multi-stage drying processes allow for the production of both rigid and semi-rigid packaging solutions tailored to product-specific protection needs.
Enhancing Structural Integrity Through Advanced Drying Methods
Packaging applications require molded pulp products to maintain durability under varying environmental conditions. By integrating enhanced drying technologies such as infrared, hot air circulation, or multi-layer metal drying, a nursery tray manufacturing machine can produce packaging that exhibits higher tensile strength and moisture resistance. This is particularly critical for industries where packaging must endure transit stresses or prolonged storage periods.
Expanding Applications in Non-Agricultural Sectors
While originally designed for seedling trays, the adaptability of a nursery tray manufacturing machine extends far beyond horticulture. Electronics manufacturers, for instance, require molded pulp trays that provide shock absorption and static resistance for sensitive components. The food industry benefits from biodegradable serving trays, protective cup holders, and molded pulp clamshell containers. Industrial sectors utilize pulp-based inserts for equipment protection, replacing foam or plastic-based packaging with environmentally responsible alternatives.
Conclusion
The evolution of nursery tray manufacturing machine technology underscores the increasing demand for customized, sustainable packaging solutions. Through mold adaptability, raw material flexibility, and advanced automation, these machines offer industries a scalable solution for eco-friendly production. As regulatory pressures and consumer preferences shift towards biodegradable packaging, optimizing nursery tray manufacturing machine capabilities will play a crucial role in shaping the future of industrial packaging.
Comments