How Coffee Cup Tray Machine Is Used in the Paper Packaging Industry
- june11433
- Feb 6
- 2 min read
The paper packaging industry relies on advanced machinery to meet the increasing demand for sustainable and efficient solutions. Among these, the coffee cup tray machine plays a pivotal role in producing molded pulp trays that secure and transport beverage cups with stability. By utilizing waste paper as raw material, this machine contributes to environmental conservation while streamlining large-scale production.
Material Processing and Pulp Formation
The operational sequence begins with raw material preparation. Waste paper, including old corrugated containers and discarded newspapers, is shredded and mixed with water to form a fibrous slurry. The coffee cup tray machine employs an integrated pulping system to refine this mixture, ensuring uniform fiber dispersion. Automated agitation and filtration remove impurities, resulting in a homogenized pulp solution with optimal consistency for molding.
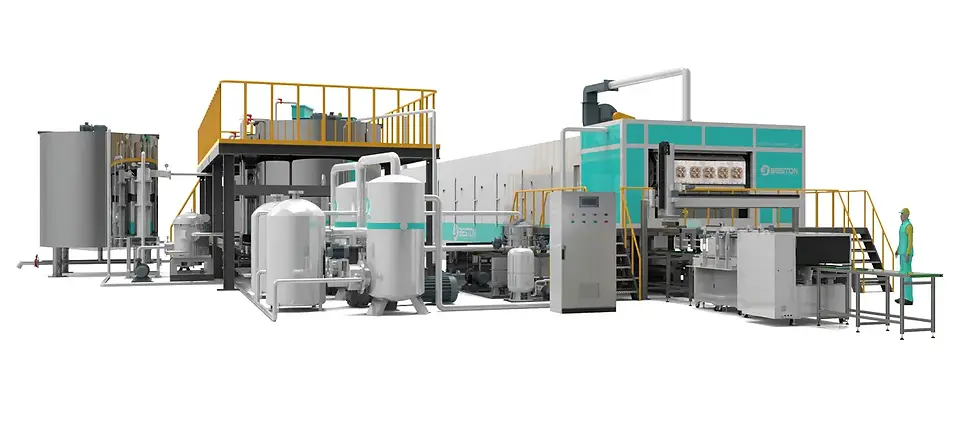
Precision Molding and Structural Integrity
Once the pulp is prepared, it undergoes a vacuum-assisted molding process. Custom-engineered molds define the tray's structural form, creating cavities designed to accommodate standard cup sizes. The molded pulp equipment utilizes negative pressure to extract excess water, enhancing the tray’s density while preserving flexibility.
High-precision mold alignment ensures dimensional accuracy, preventing defects such as uneven thickness or weakened edges. Advanced models incorporate servo-controlled mechanisms that adjust mold positioning in real time, optimizing cycle efficiency.
Drying and Thermal Stabilization
Newly formed trays contain residual moisture that must be eliminated to achieve rigidity. The drying phase employs heated air circulation or infrared radiation, expediting water evaporation. Industrial-scale coffee cup tray machines feature multi-zone drying chambers, where temperature gradients are meticulously regulated to prevent warping or brittleness.
Some configurations integrate post-drying compression, reinforcing structural integrity and ensuring stackability. This step is particularly crucial for high-load applications, where trays must endure prolonged handling without deformation.
Automation and Production Scalability
Automation enhances the efficiency of modern coffee cup tray machines. Programmable logic controllers (PLCs) regulate processing parameters, adjusting pulp viscosity, mold pressure, and drying durations dynamically. This level of control minimizes material waste while maximizing throughput.
Robotic handling systems further optimize post-production processes. Automated stacking and packaging units facilitate seamless logistics, enabling mass production without extensive manual intervention. Such innovations enhance scalability, making large-volume manufacturing economically viable for paper packaging enterprises.
Sustainability and Market Adaptation
As global regulations push for eco-friendly packaging alternatives, molded pulp trays produced by coffee cup tray machines are gaining traction. Unlike plastic carriers, these trays decompose naturally, aligning with circular economy principles. Additionally, production facilities utilizing energy-efficient drying technologies and water recirculation systems achieve lower carbon footprints.
Market trends indicate a growing preference for biodegradable solutions, prompting manufacturers to refine tray designs for enhanced durability and ergonomic handling. Customizable configurations allow businesses to tailor specifications based on branding requirements or specialized applications, ensuring adaptability in a competitive industry.
Conclusion
The coffee cup tray machine is an indispensable asset in the paper packaging industry, driving sustainable production through efficient material utilization and advanced automation. Its role in converting recycled paper into high-performance molded pulp trays underscores the industry's commitment to ecological responsibility while meeting commercial demands for functional and reliable beverage carriers.
Comments