How to Improve Production Efficiency with a High-Performance Egg Carton Machine
- june11433
- Mar 9
- 2 min read
Maximizing production efficiency is crucial for manufacturers utilizing an egg carton machine. As demand for sustainable packaging grows, optimizing output while minimizing waste and energy consumption has become a priority. A high-performance machine not only increases production speed but also enhances overall operational efficiency through automation, precision engineering, and intelligent process control.
Enhancing Automation for Consistent Output
Automation plays a pivotal role in improving the efficiency of an egg carton machine. Advanced systems integrate programmable logic controllers (PLCs) and human-machine interfaces (HMIs) to regulate production parameters with minimal manual intervention. These technologies ensure consistency in forming, drying, and stacking processes, reducing defects and material wastage.
Automated feeding mechanisms streamline raw material input, ensuring uniform pulp distribution in molds. This enhances structural integrity while maintaining production speed. Furthermore, robotic stacking systems can accelerate packaging and transport, minimizing downtime between production cycles.
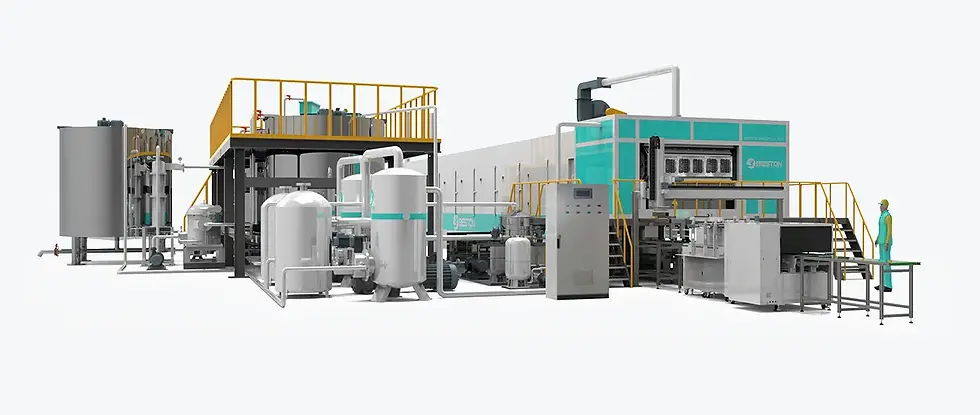
Optimizing Pulp Preparation for Quality Control
The efficiency of a pulp molding machine largely depends on the quality of the pulp mixture. Proper fiber breakdown, controlled water content, and optimized blending ratios contribute to the strength and uniformity of the final product. Investing in high-efficiency pulping units reduces processing time while achieving consistent fiber dispersion.
Implementing a closed-loop water recycling system within the pulp preparation unit can significantly cut water consumption. This sustainable approach not only conserves resources but also reduces operational costs associated with wastewater management.
Precision Molding for Reduced Defects
Molding accuracy directly affects production efficiency. A high-performance egg carton machine utilizes precision-engineered molds to ensure uniform shaping and thickness. Mold materials with high thermal conductivity improve drying efficiency, reducing cycle times.
Regular mold maintenance prevents deformations that could lead to defective cartons. Cleaning and lubricating mold surfaces minimize sticking, ensuring smooth product release and maintaining consistent production quality.
Energy-Efficient Drying Technologies
Drying is one of the most energy-intensive phases in egg carton production. High-performance drying systems, such as multi-layer conveyor dryers or integrated thermal drying chambers, enhance efficiency by optimizing heat distribution.
Infrared drying technology accelerates moisture evaporation while consuming less energy compared to conventional drying methods. Additionally, waste heat recovery systems repurpose excess thermal energy, further reducing overall energy demand. Implementing these advancements can significantly lower production costs while improving sustainability.
Streamlining Maintenance and Downtime Management
Regular maintenance schedules ensure that an egg carton machine operates at peak efficiency. Predictive maintenance technologies, such as vibration monitoring and thermal imaging, detect potential issues before they lead to machine failures.
Quick-change mold systems and modular components reduce downtime during maintenance or production transitions. Keeping spare parts readily available prevents extended disruptions, allowing for uninterrupted manufacturing.
Scalability and Production Adaptability
A high-performance egg carton machine should accommodate fluctuating production demands. Modular designs allow manufacturers to expand capacity by integrating additional molding stations or upgrading drying units. This scalability ensures that businesses can meet growing market needs without requiring a complete overhaul of existing equipment.
By focusing on automation, precision engineering, and energy efficiency, manufacturers can significantly enhance the productivity of an egg carton machine. Implementing these strategies not only boosts output but also reduces costs and environmental impact, ensuring long-term operational sustainability.
Comments