Modern Charcoal Making Machines Enable Efficient Production of Wood Charcoal
- june11433
- Aug 15, 2024
- 4 min read
In the contemporary landscape of industrial processes and environmental sustainability, the production of wood charcoal has undergone significant advancements. Modern charcoal making machines have revolutionized how wood is transformed into charcoal, enhancing efficiency, yield, and environmental management. This article delves into the intricacies of these machines, emphasizing their role in optimizing the carbonization process of wood and providing insights on how to make wood charcoal effectively.
The Carbonization Process of Wood
The carbonization process of wood is a thermal decomposition procedure conducted in the absence of oxygen. This process, also known as pyrolysis, converts wood into charcoal through the application of heat. During carbonization, complex organic materials within the wood break down into simpler compounds. The process generally involves several stages:
Drying: Initial heating removes moisture from the wood. This step is crucial as excessive moisture can affect the efficiency of the carbonization process and the quality of the final product.
Pyrolysis: As heating continues, wood undergoes pyrolysis, where it decomposes into volatile gases, tar, and a solid residue. The temperature typically ranges from 300°C to 600°C. The volatile components are driven off, leaving behind a porous, carbon-rich material.
Cooling: After the carbonization is complete, the remaining charcoal must be cooled. This step is essential to stabilize the charcoal and prevent it from re-igniting. The cooling process usually occurs in an inert environment to avoid exposure to oxygen.
Modern charcoal making machines are designed to streamline these stages, ensuring that each phase is executed with precision and efficiency.
Features of Modern Charcoal Making Machines
1. Advanced Carbonization Technology
Modern charcoal making machines utilize advanced carbonization technology to enhance the efficiency of the wood-to-charcoal transformation. These machines often feature controlled heating systems that precisely regulate temperature and heating rates. This control helps optimize the carbonization process, resulting in higher-quality charcoal with improved consistency and yield.
2. Efficient Energy Utilization
Energy efficiency is a key consideration in the design of modern charcoal making machines. Many machines incorporate advanced combustion systems and heat recovery mechanisms that minimize energy consumption. By efficiently using the heat generated during carbonization, these machines reduce operational costs and environmental impact.
3. Automated Operation
Automation plays a significant role in contemporary charcoal production. Modern machines are equipped with automated systems for feeding wood, controlling temperatures, and managing the carbonization process. This automation reduces the need for manual intervention, increases production capacity, and ensures consistent product quality.
4. Enhanced Environmental Management
Environmental concerns are central to the design of modern charcoal making machines. Many systems are designed to minimize emissions and reduce the environmental footprint of the carbonization process. Features such as smoke collection systems, gas cleaning units, and efficient dust management contribute to cleaner and more sustainable operations.
5. Versatility in Feedstock
Modern charcoal making machines are capable of processing various types of wood and biomass feedstocks. This versatility allows for the efficient conversion of different wood species into charcoal, catering to diverse industrial and commercial needs.
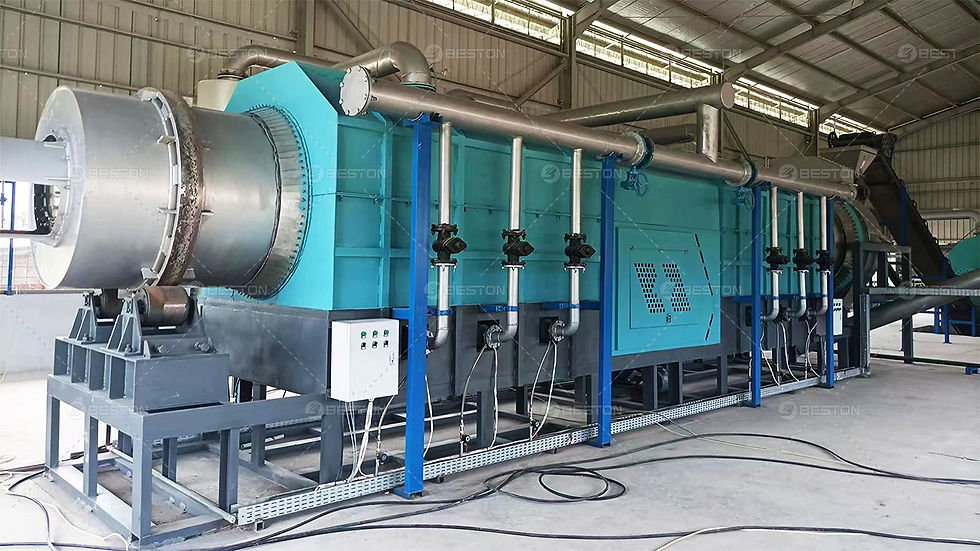
How to Make Wood Charcoal Using Modern Machines
1. Feedstock Preparation
The first step in making wood charcoal is feedstock preparation. Wood must be cut into manageable sizes and dried to reduce moisture content. Drying is essential as it prevents steam from disrupting the carbonization process. Some machines are equipped with integrated drying systems to streamline this step.
2. Loading the Machine
Once the wood is prepared, it is loaded into the charcoal making machine. Modern machines often feature automated feeding systems that ensure precise and consistent loading. This automation enhances operational efficiency and reduces labor requirements.
3. Initiating the Carbonization Process
With the feedstock in place, the carbonization process of wood begins. The machine’s heating system gradually raises the temperature to the required levels. Advanced machines allow operators to set and control specific temperature profiles to optimize the carbonization process.
4. Monitoring and Controlling
During the carbonization process, it is crucial to monitor and control various parameters such as temperature, pressure, and gas flow. Modern charcoal making machines are equipped with sophisticated control systems that provide real-time data and enable precise adjustments. This monitoring ensures that the carbonization process remains within optimal conditions.
5. Cooling and Extraction
After the carbonization is complete, the charcoal needs to be cooled. Modern machines often feature automated cooling systems that ensure gradual and controlled cooling. Once cooled, the charcoal is extracted from the machine and can be processed further or packaged for distribution.
Benefits of Modern Charcoal Making Machines
1. Increased Production Efficiency
Modern charcoal making machines significantly enhance production efficiency compared to traditional methods. Advanced technologies and automation streamline the carbonization process, resulting in higher production rates and more consistent charcoal quality.
2. Reduced Environmental Impact
The integration of environmental management features in modern machines helps mitigate the environmental impact of charcoal production. Reduced emissions, efficient energy utilization, and effective waste management contribute to more sustainable operations.
3. Improved Product Quality
The precise control over the carbonization process ensures that the resulting charcoal has a consistent quality. Higher-quality charcoal exhibits better combustion properties and is suitable for a range of applications, from industrial uses to consumer products.
4. Lower Operating Costs
Energy-efficient designs and automation reduce operating costs associated with charcoal production. Modern machines require less manual labor and use energy more efficiently, resulting in cost savings over the long term.
5. Versatility and Flexibility
The ability to process various types of wood and biomass feedstocks makes modern charcoal making machines versatile. This flexibility allows manufacturers to adapt to different market demands and feedstock availability.
Future Trends in Charcoal Production
1. Technological Advancements
Ongoing advancements in technology will likely continue to drive improvements in charcoal making machines. Innovations in automation, energy efficiency, and environmental management will further enhance the efficiency and sustainability of charcoal production.
2. Enhanced Environmental Standards
As environmental regulations become more stringent, future charcoal making machines will need to incorporate even more advanced emission control and waste management systems. The focus will be on achieving lower environmental impact and meeting higher regulatory standards.
3. Integration with Renewable Energy
The integration of renewable energy sources, such as solar or wind power, into charcoal production processes could further reduce the carbon footprint of charcoal making. Future machines may incorporate such technologies to enhance sustainability.
Conclusion
Modern charcoal making machines represent a significant advancement in the production of wood charcoal. By leveraging advanced carbonization technologies, energy-efficient designs, and automated systems, these machines offer enhanced efficiency, product quality, and environmental management. As the industry continues to evolve, ongoing innovations and improvements will further refine the charcoal production process, contributing to more sustainable and effective operations.
Comentarios