Selecting the Right Plastic into Fuel Machine: Key Factors to Consider
- june11433
- Oct 25, 2024
- 3 min read
In a world where plastic waste poses significant environmental challenges, plastic into fuel machines present an effective solution. By converting discarded plastics into useful fuels, these machines enable businesses to address both waste management and energy demands. Choosing the right machine for this process, however, requires careful consideration of specific factors that affect efficiency, output, and overall operational costs. Here’s a guide on what to assess when selecting a plastic into fuel machine.
1. Type of Plastic Waste Processed
Plastic into fuel machines vary in their ability to handle different types of plastic waste. Some machines are optimized for specific plastic types, such as polyethylene (PE), polypropylene (PP), or polystyrene (PS), while others are designed for mixed plastic waste streams. Determining the primary types of plastics available in your feedstock will guide your selection. Mixed waste processing capabilities can increase versatility, but may come at a higher operational cost due to the complexity of the processing involved.
2. Production Capacity
Capacity is a critical factor and should align with the volume of plastic waste you intend to process. Machines come in different production capacities, typically measured in tons per day. Smaller machines are suitable for limited waste streams, ideal for small-to-medium enterprises or localized operations. Larger machines, on the other hand, are intended for industrial-scale production and can handle higher volumes continuously. Analyzing expected throughput helps avoid underutilization or overextension, ensuring the machine’s output capacity matches operational needs effectively.
3. Automation and Operational Efficiency
Automation levels in plastic to oil machine can significantly influence labor requirements and process efficiency. Machines range from semi-automatic to fully automated systems. Fully automated machines reduce manual intervention, streamline production, and enhance overall efficiency. However, these systems may come with a higher price tag. For businesses seeking cost-effective solutions, semi-automated machines may offer a balanced compromise between cost and operational demands. Automated machines are ideal for continuous, large-scale operations, where reducing human oversight can lead to significant savings over time.
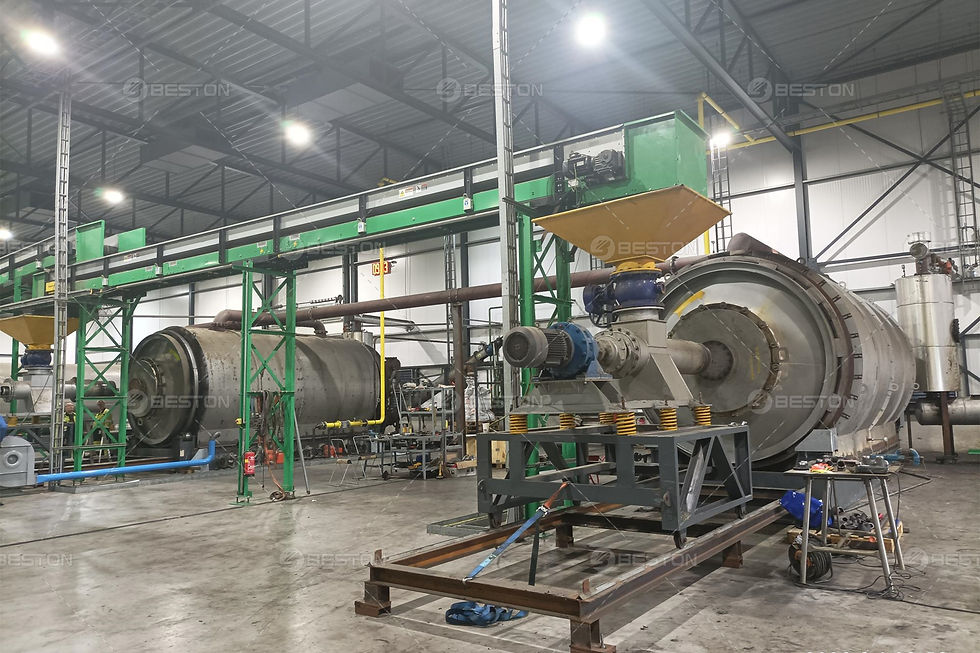
4. Energy Consumption and Fuel Efficiency
Given that plastic pyrolysis involves high-temperature processes, energy consumption is an essential factor. Machines with energy recovery systems can convert byproduct gases back into fuel for the heating system, making the process more sustainable and reducing external fuel dependency. Assessing the machine’s fuel efficiency and energy recovery potential can provide insights into operational costs and energy savings, particularly for continuous or industrial-scale machines.
5. Environmental Compliance
When selecting a plastic into fuel machine, it’s essential to consider environmental regulations and compliance. Most machines are equipped with pollution control systems that reduce emissions and handle hazardous byproducts. Choosing a machine that meets local and international environmental standards not only ensures compliance but also contributes to corporate sustainability goals. Proper filtration and gas treatment systems are critical, especially for businesses located in regions with stringent environmental regulations.
6. Byproduct Utilization
Plastic into fuel machines produce several byproducts, including pyrolysis oil, carbon black, and non-condensable gases. Machines with built-in separation and refinement systems allow for the collection and resale of these byproducts, potentially creating additional revenue streams. Understanding the market for these byproducts and evaluating a machine’s ability to handle, refine, and store them can impact overall profitability and expand business opportunities.
7. Cost Considerations and Return on Investment
The initial cost of a plastic into fuel machine varies widely based on capacity, level of automation, and additional features. While higher-end models may offer greater efficiency and reduced labor costs, it’s essential to assess whether the long-term savings and potential revenue justify the investment. Factors like energy savings, byproduct resale, and reduced waste disposal costs can all influence the return on investment. A thorough cost-benefit analysis will help determine the most economically viable option.
Conclusion
Choosing the right plastic into fuel machine involves a careful balance of production needs, budget constraints, and environmental considerations. By evaluating the type of plastic waste, production capacity, automation, and compliance standards, businesses can select a machine tailored to their specific requirements. With the right machine, plastic waste becomes a valuable resource, supporting both environmental goals and economic growth.
Comentários